ラジカル窒化
ラジカル窒化は表面をほとんど変化させません。チタンコーティングとの複合が効果的です。
※日本コーティングセンター(株)製品
ラジカル窒化法(J-ナイト)
ラジカル窒化とは
従来の窒化法の問題点を改善するために、プラズマ窒化反応理論を基礎として開発された、新しいプラズマ窒化法です。この窒化法は高速度工具鋼や合金工具鋼等の高合金鋼の処理に適しています。その特徴を以下に示します。
- 表面状態をほとんど変化させません。
- 化合物層を形成せず拡散層のみを形成できます。
- 寸法変化を非常に小さく抑えることができます。
- これらの特徴により処理後の後加工が不要となります。
- 400から560℃の広い範囲で処理できます。
- 処理表面に直接PVD法などで硬質膜を形成できます。
これらの特徴によって、金型や、機械部品などの耐摩耗性が向上し、寿命を延ばし生産性を向上させることができます。また、ラジカル窒化と硬質膜形成を組み合わせた複合硬化処理を行うことにより、硬質膜の特性を大幅に向上することができます。
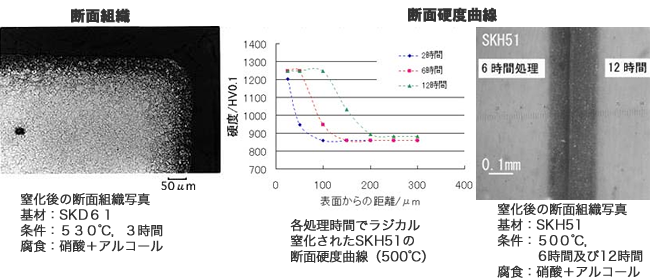
ラジカル窒化適用材料例
【合金工具鋼】SKD61、SKD11(高温戻し)
【プリハードン鋼】HPM1,HPM50, NAK55,NAK80
【高速度工具鋼】SKH51,SKH57,HAP50
【構造用合金鋼】SACM645,(SCM)
ラジカル窒化と他の窒化法による表面粗度の変化と窒化状態
鋼種 | 処理法 | 表面硬度(HVO.1) | 化合物層(μm) | 拡散層(μm) | 表面粗度(Ra) | 表面粗度(Rmax) |
---|---|---|---|---|---|---|
SKD61 | 未処理 | 592 | - | - | 0.02 | 0.05 |
ラジカル窒化 | 1230 | 0 | 130 | 0.04 | 0.2 | |
ガス軟窒化 | 894 | 12 | 130 | 0.18 | 2.88 | |
イオン窒化 | 1250 | 8 | 100 | 0.14 | 0.98 |
ラジカル窒化応用例
”ラジカル窒化”を用いると、射出成形、プレス成形等で使用される金型、各種部品の寿命が著しく延びます。特にプリハードン鋼使用の金型では、寸法変化がないため最適です。当社では金型以外にも治具などの各種機械部品へのラジカル窒化の適用を進めております。
ラジカル窒化と複合硬化処理の応用例と効果
種類 | 種類 | 処理 | 効果 |
---|---|---|---|
樹脂型 | キャビティコア,ピン | ラジカル | ・窒化後の研磨不要 ・型寿命:約5倍(未処理品と比較) |
プレス型 | 粉体(フェライト) | ラジカル | ・型寿命:2~5倍 |
鍛造型(鋼塊)・絞り型(鋼板)・曲げ型(鋼板) | ラジカル+TiCN,CrN | ・対面圧性向上 ・膜剥離発生が大幅減少 ・型寿命:2~3倍(成膜処理品と比較) |
|
トリミングダイス・パンチ(鋼板) | ラジカル+TiCN | ・CVD品より熱変形小 ・ダイス寿命:2~3年 (成膜処理品と比較) |
|
成型ロール | 転造・フォーミング・バニシング | ラジカル+TiCN | ・耐面圧性向上 ・ロール寿命:2~3倍 (成膜処理品と比較) |
射出成形機関連 | スクリューバレルなど | ラジカル+TiN | ・窒化後の研磨が不要 ・寸法精度向上 ・離形成向上、硬度粘性向上 |
押出機関連 | ゴム押出ダイス | ラジカル | ・型寿命:10倍(未処理品と比較) |
機械部品(合金工具鋼) | 耐摩耗治具・機械部品 | ラジカル+TiN,TiCN | ・寿命:2~5倍 (成膜処理品と比較) |
ラジカル窒化装置及び処理工程の概略
装置は、真空チャンバー、真空ポンプ、自動圧力制御装置、ガス制御装置、直流電極、プラズマ発生用の直流電源、外部加熱炉、そして冷却装置から構成されます。処理内容は、まず処理部材を脱脂洗浄後、真空チャンバー内の直流電極上に置き、排気(真空)、昇温後、水素とアンモニアの混合ガスを反応ガスとして炉内に導入します。その後、処理部材の表面にプラズマを発成させ、ラジカル窒化処理後、冷却します。本処理は、反応性の高いプラズマを作る事が出来るため、化合物層の面荒れによる表面の変化がない、そして均一で深い拡散層のみを作る事が出来ます。
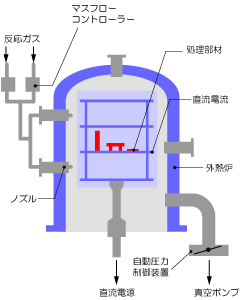
ラジカル処理のメリット
硬度低下、歪みがない
450℃から530℃前後で処理。よって、SKD,SKH等であれば、残留応力が無ければ硬度低下、歪みは発生しない。
処理後の磨きが不要
イオン窒化、ガス窒化は表面に化合物層ができ方面が荒れるため、処理後バフ磨きが必要である。本処理は化合物層が出来ず、表面の面荒れがないため、バフ磨きが不要。
剥離がない
窒化は表面皮膜処理と異なり、拡散浸透型のため膜の剥離がない。
複合処理が可能
イオン窒化の場合、表面の化合物層を完全に取り除く必要があったが、本処理はそのままコーティング可能。
窒化深さが均一
従来、イオン窒化の場合、先端部分やコーナー部が重点的に窒化される傾向があったが、本処理の場合均一である。
特にメリットが高いと考えられるもの
【A.樹脂金型・スクリュー】
耐摩耗に効果大。PVD/TiN等と併用するとより効果がある。(耐摩耗、耐腐食、離型性)残留応力が無ければ寸法変化は発生しない。窒化後のバフ研磨等磨きが必要ないため工数削減が可能(コストダウン)
【B.機械部品等】
浸炭後研磨、窒化後研磨を行っている部品、また表面の光輝性を維持しなければならない部品(成形機のスクリュー、ピストンリング、治具等)は後工程を省略できる。
各種表面硬化処理の比較
★印は弊社にてコーティングサービスを承っております
CVD/TiC★ | PVD/TiN★ | TD | イオン窒化★ | ガス窒化 | ラジカル窒化★ | |
表面硬度 (HV) | 3800-4000 | 1700-2500 | 2000-3000 | 900-1200SKD SKH | 900-1200SKD SKH | 900-1200SKD SKH |
膜 厚(μm) 有効硬化深さ | 7/10 | 2/4 | 7/10 | 10/300 | 10/00 | 10/300 |
処理温度(℃) | 900-1000 | 200-550 | 1000-1200 | 350-570 | 500-540 | 350-550 |
変形(歪み) | C | A | D | A | B | A |
付き回り性 | A | C | B | C | A | B |
膜の均一性 | A | A | C | B | A | A |
密着性 | A | B | A | A | A | A |
化合物層の有無 | – | – | – | 有 | 有 | 無 |
IP窒化(J-ナイトIP窒化)
ステンレス鋼やオーステナイト系耐熱鋼向けに開発された窒化処理です。ラジカル窒化と同じように表面状態をほとんど変化させず、表面に高耐食性の化合物層(Me4-N)を形成します。また、このうえに直接PVD処理を行うことで、よりポテンシャルの高い複合硬化処理を施すことができます。
SUS420J2処理前後の比較
窒化前後の表面粗度(μm)、表面硬度(HV0.1)、全硬化層(μm)
処理前 | IP窒化A | IP窒化B | ガス窒化 | |
Ra | 0.04 | 0.52 | 0.08 | 0.44 |
Rmax | 0.10 | 0.52 | 0.64 | 5.84 |
表面硬度 | 300 | 1230 | 1250 | 約1000 |
全硬化層 | – | 40 | 80 | 120 |
SUS420J2処理前後の耐食性比較
塩水噴霧試験(JIS Z 2371、35℃5%食塩水)後のレイティングナンバ
無処理 | IP窒化A | IP窒化B | ガス窒化 | |
1時間後 | – | – | – | 発錆 |
2時間後 | 発錆 | – | 発錆 | ↑ |
4時間後 | ↑ | – | ↑ | ↑ |
6時間後 | ↑ | 発錆なし | ↑ | ↑ |
24時間後 | 9-3 | 発錆9.5-2 | 8-1 | 7-1 |
SUS304処理前後の耐食性比較
塩水噴霧試験(JIS Z 2371、35℃5%食塩水)
無処理 | IP窒化C | |
144時間後 | 発錆なし | 発錆なし |
イオン窒化
イオン窒化法とは、従来のガス窒化法、塩浴窒化法、ガス軟窒化法とは異なり、プラズマによって窒素イオンが処理面に衝突し、拡散されることによって窒化する表面硬化法です。
熱歪僅少
グロー放電によって、イオン化した窒素を注入・拡散作用で処理面を窒化させるため、低温処理が可能です。そのため、処理物の熱歪みがほとんどありません。
清浄仕上げ
真空中での硬化処理です。処理物の表面は極めて清浄で、後処理がいりません。同時に表面粗さの低下もほとんどありません。
窒化層のコントロール
他の窒化法ではできないγ’単相の化合物相生成、層厚のコントロール、さらに深い拡散層を得ることができます。また、必要な個所のみへの部分窒化も可能です。
非鉄金属への窒化
チタン、チタン合金など非鉄金属への窒化ができます。
複合硬化処理(J-coatα)特許第1994196号、第2773092号
ラジカル窒化もしくはIP窒化を各種PVDコーティングの下地に施すことにより、膜の耐久性を大幅に向上することができました。
下地を硬くすることにより、膜の割れ、剥がれを抑えることが可能になります。そのため、耐摩耗性、耐腐食性とも大幅に向上し、驚異的な寿命を追求することが可能となります。
この複合硬化処理は、それぞれの相乗効果により次世代のPVD処理と評価されています。
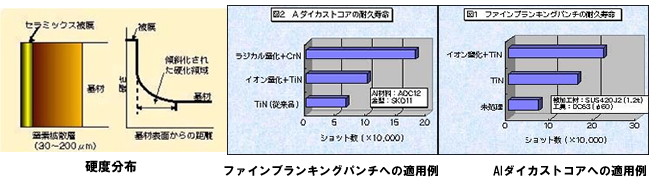
概要(ラジカル窒化との複合処理)
図のように主に窒化、浸炭といった拡散硬化法を利用して、コーティングの基材に傾斜化された効果領域を形成し、機械的強度を向上させ、被膜の持つ特性と相乗効果を生み出すものです。硬度分布、適用事例を参照ください。
概要(IP窒化との複合処理)
SUS304機械部品への適用例です。これまで、定期的にTiNコーティングが必要であった部品が、下地の補強効果でメンテナンスフリーとなりました。